Road tests carried out under adverse conditions repeatedly demonstrated problems with the durability of the exhaust system fixing. What was needed was a fastening solution for a rubber buffer to retain the exhaust, including process monitoring. The exhaust system concerned is fitted in a mid-range vehicle of a major automotive manufacturer. The challenge was to insert two blind rivets under process monitoring.
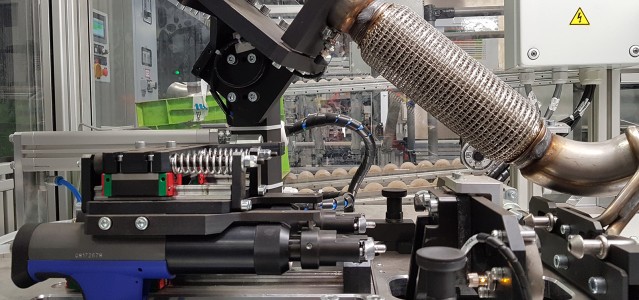
Customized solution
From plan to production
The process monitoring was to ensure that the rivet chosen specifically for this application was correctly inserted. During the setting process, all the relevant predefined parameters had to be achieved and the inspection results transferred to the GESIPA® databank for storage.
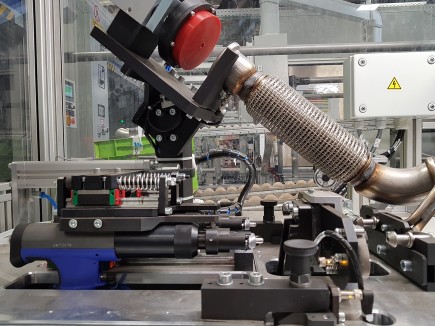
One critical aspect of correct rivet setting and overall bond durability, even in unfavourable weather conditions, surrounds the exact positioning and fixing of the components. Before setting the blind rivet, it must be ensured that a security or support element is correctly in place. A system for this was developed between GESIPA® and one of their long-term partners in system construction, Herrtwich & Co. of Rodgau, Germany. A manually operated linear axis system was developed in close collaboration with Herrtwich and fitted to an assembly unit. It was thus possible to ensure that the exhaust system was exactly positioned to enable the blind rivets to be correctly set every time.
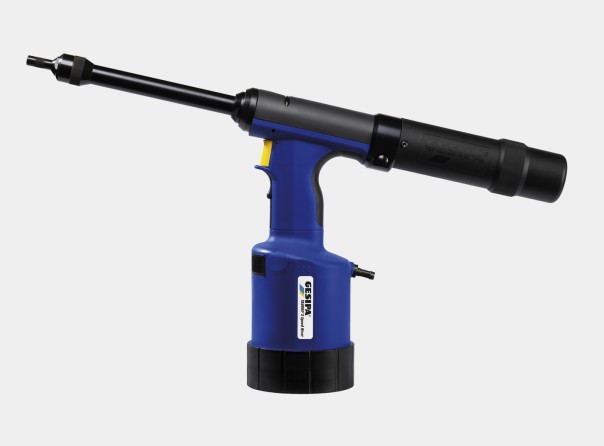
A further challenge was process monitoring of the setting operation in a blind bore. The normal setting procedure is not possible in such conditions, because the rivet cannot form a closure head. Following considerable deliberation, the GESIPA® project team turned to the TAURUS® C range for inspiration; a system which has been tried and trusted across numerous branches of industry for over fourteen years now. It became obvious that this offered a reliable, economical answer to an application where a fully-automated system could not yet pay for itself with the quantities called for.
Thanks to the fixture supplied by GESIPA®, the necessary high quality standard demanded by the customer could be guaranteed. Indeed so happy was the customer with the output rate and quality from the pilot plant that meanwhile a further seven similar units have been installed in the plant concerned.