Creative minds and high expertise
Eight creative thinkers launched the development project at SFS. Intensive thought showers during a dedicated workshop provided a wide range of product concepts. Two months later, 27 different ideas were critically evaluated, with just two making it through to the final round.
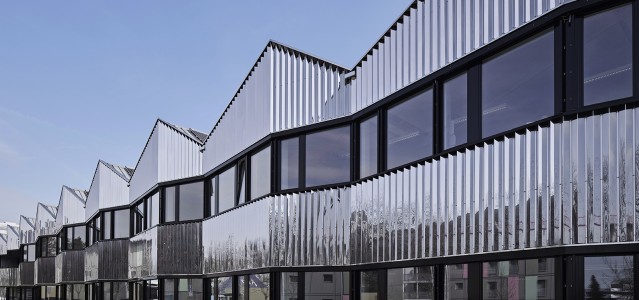
A screw sets new standards
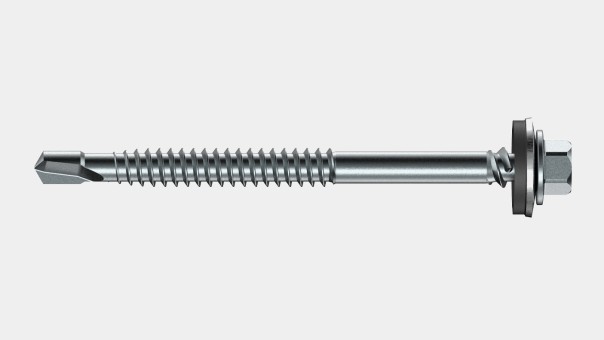
From prototype to SXC5
The project team developed 15 different variants for each of the two competing designs, with the next step being to produce and trial 30 different prototypes: an essential capability available to SFS in-house. In up to 20 separate production steps the individual drilling screws were manufactured and put to the test using realistic conditions with the sole aim of increasing the key technical parameters.
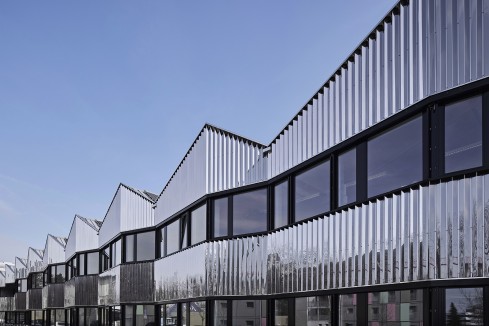
An innovative fastener with countless advantages
Achieving a larger flange and head diameter were clearly the least problematic issues; likewise, the project team soon managed to create the required asymmetric threading, visible to the naked eye, by working closely with manufacturing colleagues. The real challenge lay in the micro-metre adjustments required. Nevertheless, these creative minds managed to achieve a massive 50% increase over the previous tear-out performance. The thread geometry of an individual SXC5 could be adjusted to offer the customer two savings: either reducing the number of fastener positions and/or optimising the thickness of the substructure. Both options translate into considerable savings for the customer.